Since the 1990s, satellite navigation systems have been integrated into many aspects of our lives. However, it is important to have reliable positioning alternatives for when this tool is not available. These advancements mostly focus on military innovation and defense, ensuring the movement of aircraft, vehicles, and troops in electronic warfare environments.
What are Global Navigation Satellite Systems?
Global Navigation Satellite Systems (GNSS) are positioning and navigation systems that use a network of satellites in orbit around the Earth to determine the precise location of a receiver anywhere in the world. These systems are designed to provide three-dimensional positioning information of an object, its speed of movement, and the time it is located at a specific place with very high accuracy.
The most well-known and widely used GNSS is the Global Positioning System (GPS) developed by the United States. There are also other GNSS systems such as Russia's GLONASS, the European Union's Galileo, and China's Beidou. These systems operate through a constellation of satellites that transmit navigation signals to receivers on Earth. These receivers use the signals received from multiple satellites to calculate their position with an accuracy of a few meters or even centimeters, depending on the quality of the receiver and the number of signals received.
GNSS systems have revolutionized the way we navigate and move around the world. They are currently used in a wide range of civilian, industrial, and military applications, including maritime navigation, aviation, mapping, emergency services, and precision agriculture.
Alternatives to GNSS
When it is not possible to use Global Navigation Satellite Systems, either due to their unavailability or their unreliability, such as in dense urban environments, near ports with a saturation of positioning equipment that hinders ship docking, or in cases of electronic attacks, there are a number of experimental alternative technologies.
One of these alternatives is inertial navigation, which uses sensors such as accelerometers and gyroscopes to measure changes in velocity and the orientation of a moving object. These sensors allow determining the relative position and trajectory of the object, although they can accumulate errors over time as measurements accumulate.
Another alternative is the use of terrestrial beacons and radio frequencies. This method is based on receiving signals emitted by ground stations, which contain position and time information. Receivers can measure the time difference between the signals and calculate the position. However, this approach requires considerable terrestrial infrastructure and a good understanding of the location and characteristics of the beacons.
Similarly, there are systems based on radio direction finding, which use directional antennas to measure the direction of arrival of radio signals from known transmitters. However, their range is limited to very specific areas and depends entirely on the available infrastructure.
These alternatives have limitations in terms of accuracy and reliability compared to GNSS systems, so their application depends on the context and specific needs of each case.
With the aim of offering a precise and improved alternative for positioning and navigation without relying on GNSS, Skylife Engineering has coordinated the R&D and innovation project OPTIMISE. The main objective is a research effort to enhance positioning, navigation, and timing in areas where access to GNSS systems is not available, through an innovative architecture that combines data from different signals and sensors.
The OPTIMISE platform merges various technologies for PNT (Positioning, Navigation, and Timing), which, when combined, seek to achieve a more reliable result. In addition to using more modern and effective sensors, a significant part of the project seeks to test a wide range of tools based on emerging technologies for specific situations, along with central software that integrates and fuses them to obtain a more accurate and robust solution.
The technologies involved in the project include:
- Feasibility study to bring magneto-inertial technology to the aerial platform.
- Positioning system based on signals of opportunity (SoOp) with parallel processing.
- Advanced integration of synthetic aperture radar (SAR) on aerial platforms to test the technological feasibility of the system.
- MEMS atomic clock and atomic inertial measurement unit (IMU).
- Stellar navigation system.
Firstly, several workshopswere conducted with experts throughout 2021 to define requirements and constraints, as well as to study the current state of available technologies and methods. Based on this, the scenarios and roadmapfor the development of the different systems were defined. Subsequently, prototypes were designed for each technology, and from June 2022 to April 2023, various integration and validation tests were carried out on both land and in-flight at the Žilina airport in Slovakia. To measure the results, a reference trajectory for the aircraft was defined.
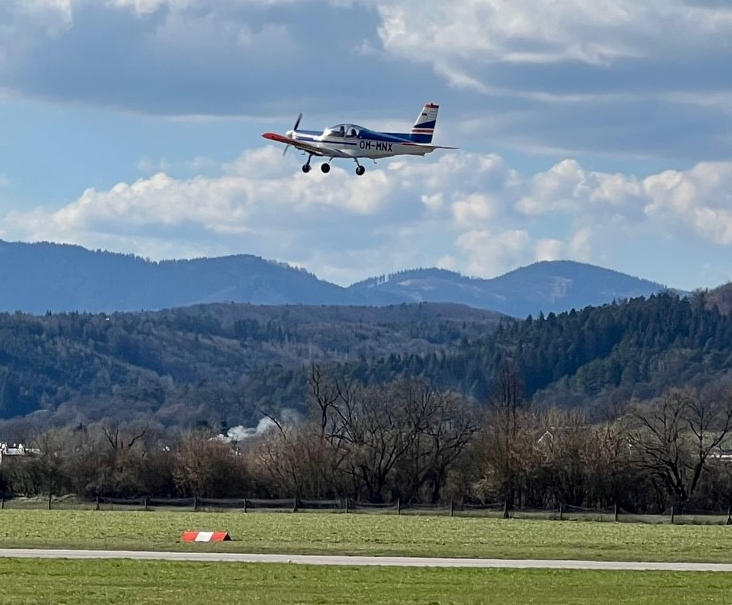
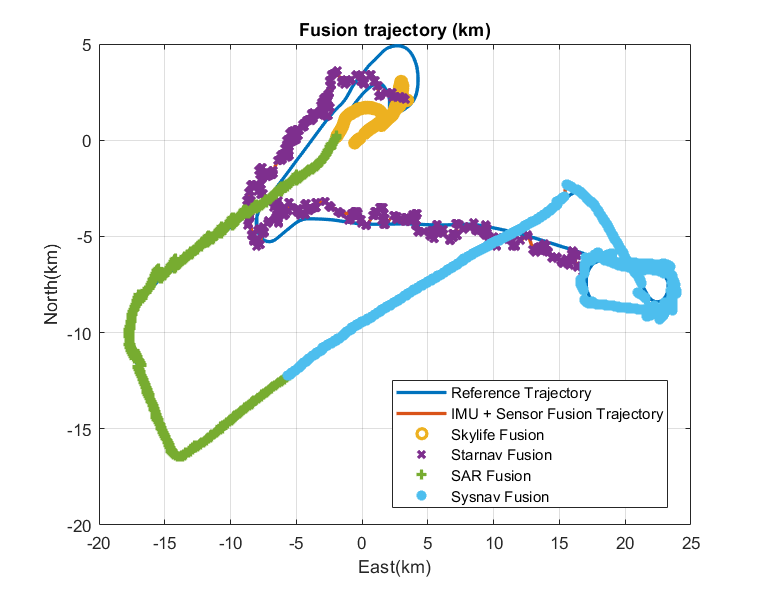
After the flight tests, an evaluation of the different technologies was conducted based on sensor reliability criteria, fusion accuracy, latency, update rate and data availability, yielding the following result:
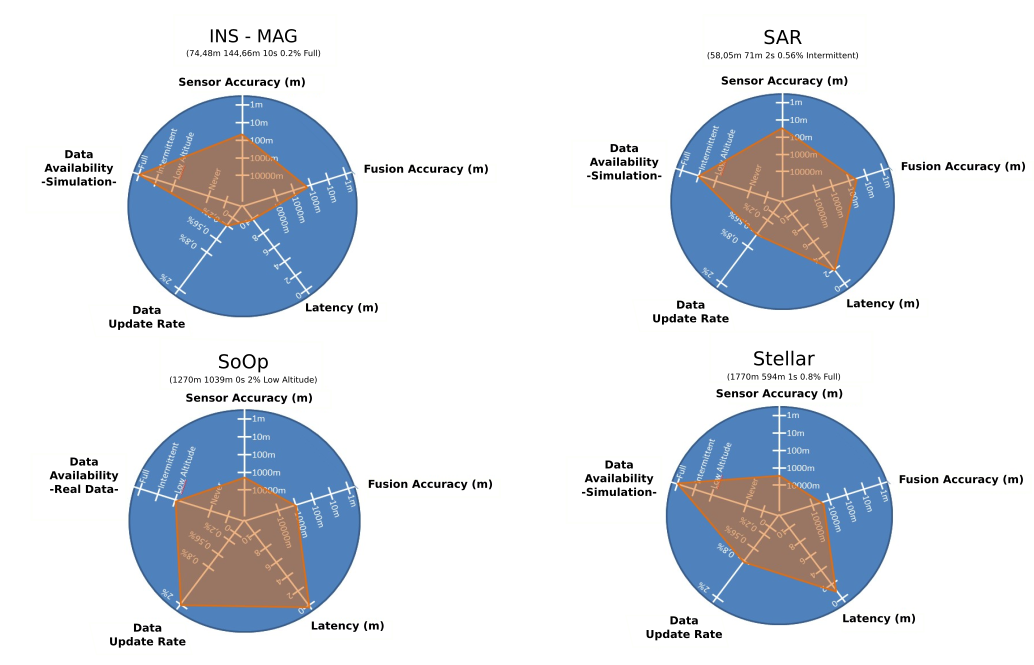
OPTIMISE is another testament to how Skylife actively participates in innovation and the development of new technologies in fields such as PNT technology development in European Union defense programs. In this project, coordinated by Skylife, participants included MBDA, Sener Aeroespacial, ONERA - The French Aerospace Lab, SYRLINKS, STARNAV, SYSNAV, the University of Žilina, and AICIA (Andalusian Association for Research and Industrial Cooperation).
OPTIMISE is part of the European Union program called PADR (Preparatory Action on Defense Research) (GA No 884134), and its results will be taken into account for the allocation of funds for research from the European Defense Fund (EDF).